PHA: A biopolymer whose time has finally come
Amid the growing plastic waste crisis, producers of polyhydroxyalkanoate think the world is ready for their biodegradable polymers
FROM:
At Silicon Valley Clean Water in Redwood City, California, an installation assembled from a shipping container, plastic piping, brackets, and a small steel reactor is testing technology that could lead to a more sustainable plastic.Mango Materials has run this pilot facility since 2015. Raw biogas—which contains methane, carbon dioxide, and hydrogen sulfide—from the water treatment plant bubbles through the reactor. Bacteria in the vessel metabolize the methane into the biopolymer poly(3-hydroxybutyrate), or PHB.“Once they are the fattest, happiest organisms possible, we have to break open their cells and get the polymer,” says Anne Schauer-Gimenez, Mango’s vice president of customer engagement. The polymer that Mango extracts, about 250 kg of it per year, is tested in applications such as fibers and packaging for beauty care products.Mango is among the dozens of firms attempting to create an industry around polyhydroxyalkanoates (PHAs), a class of biodegradable, biobased polymers. Executives with these firms are well aware of the PHA firm Metabolix , now called Yield10 Bioscience, which burned through hundreds of millions of dollars before it failed in PHAs 3 years ago. But Metabolix may have been ahead of its time.Public awareness of the mounting crisis in plastic waste, especially the plastic that ends up in the ocean, is rising. Governments are imposing bans on single-use plastics, and large consumer product companies are clamoring for solutions. A polymer that can disappear from the environment altogether might just be what the world needs.PHAs have a lot on their curriculum vitae that suggests they’re perfect for this moment. They occur in nature. Bacteria use them to store energy when they lack enough nutrients to reproduce. Scientists have found more than 150 PHAs with different polymer structures. The kind of bacteria and what they are fed—be it sugars, starches, glycerin, triglycerides, or methane—determines the PHA produced.Biodegradability is the most intriguing property of PHAs. The largest-volume biobased polymer, polylactic acid, also breaks down, but only in an industrial composting facility. PHAs will biodegrade in ambient environments, even in the ocean.The physical properties of PHAs are often compared to polyolefins such as polyethylene and polypropylene. Indeed, many of the applications that companies have in mind for the polymers—single-use products like food packaging, straws, and cutlery—currently belong to polyolefins. The New Plastics Economy: Rethinking the Future of Plastics, a seminal 2016 report by the Ellen MacArthur Foundation, even lists PHAs as potential substitutes for polyolefins as well as polyethylene terephthalate, polystyrene, and polyvinyl chloride.“There is such a wide array of different PHAs that, depending on what kind of PHA you produce, you can get similar properties to each one of those other materials,” says Phil Van Trump, chief technology officer for the PHA developer Danimer Scientific.An important distinction in PHAs is between short-chain and medium-chain polymers. Short-chain PHAs, such as PHB, are made of smaller monomers. Medium-chain PHAs, such as poly(3-hydroxybutyrate-co-3-hydroxyhexanoate) (PHBH), are made of larger ones.“Pendant chains hanging off your molecule will influence your properties,” says Jan Ravenstijn, an independent biopolymer consultant and veteran of the polymer makers DSM and Dow. The short-chain polymers are more crystalline—hard but brittle. The medium-chain ones are tougher and more resilient.Ravenstijn says PHAs are best suited for those applications where “biodegradation is a must,” such as products that “inevitably end up in the environment.” He points to slow-release fertilizer coatings made of synthetic polymers like polyurethanes that don’t biodegrade.In another such application, the Italian PHA firm Bio-on recently launched a line of sun creams, called MyKai, with Unilever. The creams incorporate micropowders made with Bio-on’s PHB that can improve the effectiveness of ultraviolet light–reducing ingredients.“It is the perfect molecule for that kind of application,” Diego Torresan, Bio-on’s business development manager, says of PHB. The company makes the PHB from molasses and by-products of sugar beet production at its demonstration plant near Bologna, Italy. The facility started up last year with 1,000 metric tons (t) of annual capacity, which is dedicated to specialty products such as the powders for Unilever and microbeads for other personal care applications.
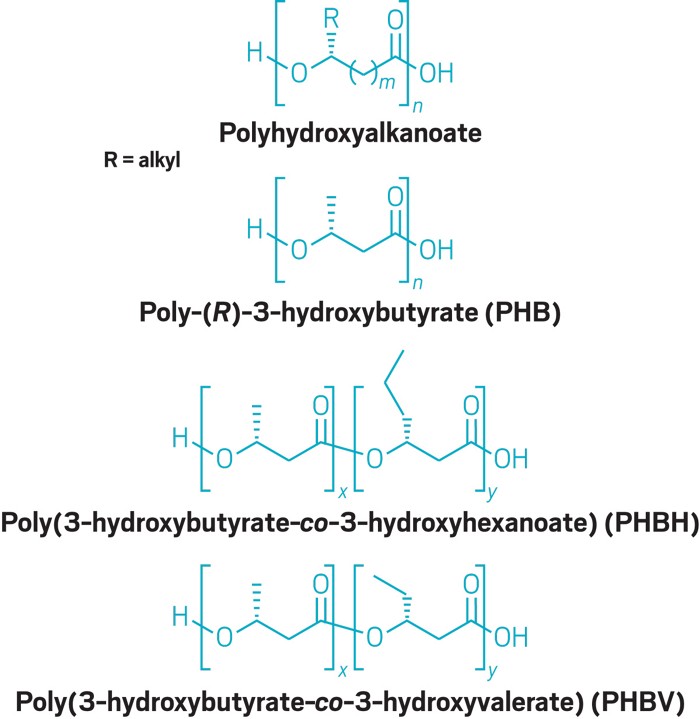
Bio-on has been busy developing other PHA applications as well. Late last year, it formed a joint venture, called Zeropack, with the Italian fruit distributor Rivoira to commercialize PHB packaging for fresh fruit and vegetables. Bio-on is also working on applications such as toys, auto parts, and furniture.
Danimer has PHA technology that it acquired from Procter & Gamble in 2007. The company is already a large compounder of polylactic acid, operating 50,000 t per year of reactive extrusion capacity. Its pilot plant in Bainbridge, Georgia, makes about 10 t of PHAs per month from rapeseed oil.
Van Trump says Danimer’s polymer formulation expertise, plus its versatile medium-chain PHA technology, allows it to pursue ambitious applications. For example, with PepsiCo’s Frito-Lay division, Danimer has been developing a snack bag material to replace the polypropylene film currently used. It is working on PHA water bottles with NestlĂ©.
With such heavy interest in their materials, PHA companies are ready to take the next step: building commercial plants.
Metabolix made it to this stage a decade ago, and its failure remains a cautionary tale for the rest of the industry. In 2010, the company started up a PHA joint venture with Archer Daniels Midland (ADM) in Clinton, Iowa, that boasted 50,000 t of annual capacity.
ADM shuttered the plant 2 years later due to slow adoption of the materials by customers. The plant couldn’t even meet a milestone of 500 t per year of sales. ADM had to write off $339 million. Metabolix struck out on its own but had to sell its technology to the South Korean firm CJ CheilJedang for $10 million in 2016. It changed focus to agricultural technology and changed its name to Yield10.
“They built too much capacity,” Ravenstijn says. “There was no market. And developing a market for a new polymer is something that goes step by step. My advice would always be to build demand ahead of capacity.” This, he believes, is the approach current PHA players are taking.
Bio-on has been developing a market for PHAs since it bought technology for making PHB and other PHAs from the University of Hawaii in 2007. “When we started, the environment was not ready to take on PHA,” Torresan says. That’s now changed, he says, because of greater customer and brand owner awareness of plastic waste.
Torresan also sees regulatory drivers, such as the European Union’s requirement to find sustainable alternatives by 2021 to fossil-fuel-based single-use plastic items such as cotton swab sticks, cutlery, plates, and straws. “It is among, if it is not the sole, solution for those kinds of applications,” he says of PHAs.
“It’s a perfect storm that is brewing,” Danimer’s Van Trump says. “There is more demand then there was 3 or 5 years ago.” The company demonstrated PHA straws last year. “Due to the plastics bans and folks not liking paper straws so much, there’s a lot of interest,” he says.
In Winchester, Kentucky, Danimer is building what will be the world’s largest PHA plant when it starts up in October with about 8,000 t per year of capacity. The $36 million project involves the conversion of an idle algae fermentation facility.
Bio-on’s model is not to build large capacity but to license its technology. While its demonstration plant near Bologna is making specialty products for Bio-on’s own sales, it is also meant to prove the process for licensees.
The company has inked a number of PHA licenses already. The family-owned company SECI plans to build a 5,000 t per year plant in Italy. The Russian firm TAIF took out a license to build a 10,000 t plant in the Republic of Tatarstan. Bio-on has also licensed its process to companies in France, Spain, and Mexico.
A few other firms are jumping into the business as well. Japan’s Kaneka is set to have 5,000 t of capacity for PHBH in Takasago, Japan, by the end of the year. CJ CheilJedang, with Metabolix’s technology in hand, plans to either build a pilot plant or outsource small-scale PHA production, Sim Do Yong, of the company’s business development team, tells C&EN. The company aims for commercial production in 2022.
RWDC Industries was cofounded by Daniel Carraway, who also founded Danimer but later left the company. It has raised $35 million from investors and plans to build a PHA plant in Athens, Georgia.
Mango Materials, meanwhile, has nearly completed a demonstration unit at the Redwood City site where it operates the pilot plant. The unit will run continuously and produce more than 100 kg of material per week. “We can derisk a few components of the technology while actually producing meaningful volumes of material to use it for applications,” Schauer-Gimenez says.
A commercial plant, she acknowledges, is still a few years away. Mango will soon close a fundraising round, Schauer-Gimenez says, with investors who appreciate the amount of time needed to get the technology off the ground.
“Patient capital is what’s really key for us right now,” she says. “We’re not an iPhone app. Your return doesn’t come overnight.”
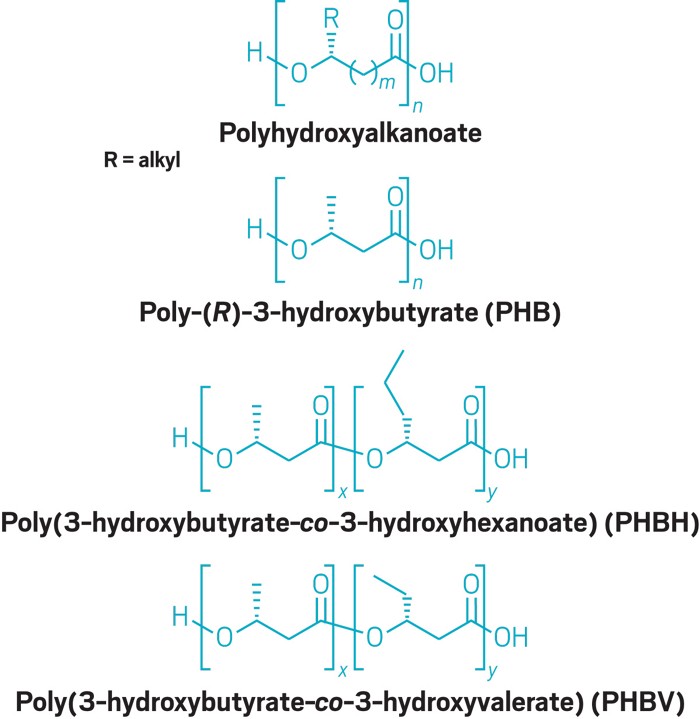
Bio-on has been busy developing other PHA applications as well. Late last year, it formed a joint venture, called Zeropack, with the Italian fruit distributor Rivoira to commercialize PHB packaging for fresh fruit and vegetables. Bio-on is also working on applications such as toys, auto parts, and furniture.
Danimer has PHA technology that it acquired from Procter & Gamble in 2007. The company is already a large compounder of polylactic acid, operating 50,000 t per year of reactive extrusion capacity. Its pilot plant in Bainbridge, Georgia, makes about 10 t of PHAs per month from rapeseed oil.
Van Trump says Danimer’s polymer formulation expertise, plus its versatile medium-chain PHA technology, allows it to pursue ambitious applications. For example, with PepsiCo’s Frito-Lay division, Danimer has been developing a snack bag material to replace the polypropylene film currently used. It is working on PHA water bottles with NestlĂ©.
With such heavy interest in their materials, PHA companies are ready to take the next step: building commercial plants.
Metabolix made it to this stage a decade ago, and its failure remains a cautionary tale for the rest of the industry. In 2010, the company started up a PHA joint venture with Archer Daniels Midland (ADM) in Clinton, Iowa, that boasted 50,000 t of annual capacity.
ADM shuttered the plant 2 years later due to slow adoption of the materials by customers. The plant couldn’t even meet a milestone of 500 t per year of sales. ADM had to write off $339 million. Metabolix struck out on its own but had to sell its technology to the South Korean firm CJ CheilJedang for $10 million in 2016. It changed focus to agricultural technology and changed its name to Yield10.
“They built too much capacity,” Ravenstijn says. “There was no market. And developing a market for a new polymer is something that goes step by step. My advice would always be to build demand ahead of capacity.” This, he believes, is the approach current PHA players are taking.
Bio-on has been developing a market for PHAs since it bought technology for making PHB and other PHAs from the University of Hawaii in 2007. “When we started, the environment was not ready to take on PHA,” Torresan says. That’s now changed, he says, because of greater customer and brand owner awareness of plastic waste.
Torresan also sees regulatory drivers, such as the European Union’s requirement to find sustainable alternatives by 2021 to fossil-fuel-based single-use plastic items such as cotton swab sticks, cutlery, plates, and straws. “It is among, if it is not the sole, solution for those kinds of applications,” he says of PHAs.
“It’s a perfect storm that is brewing,” Danimer’s Van Trump says. “There is more demand then there was 3 or 5 years ago.” The company demonstrated PHA straws last year. “Due to the plastics bans and folks not liking paper straws so much, there’s a lot of interest,” he says.
In Winchester, Kentucky, Danimer is building what will be the world’s largest PHA plant when it starts up in October with about 8,000 t per year of capacity. The $36 million project involves the conversion of an idle algae fermentation facility.
Bio-on’s model is not to build large capacity but to license its technology. While its demonstration plant near Bologna is making specialty products for Bio-on’s own sales, it is also meant to prove the process for licensees.
The company has inked a number of PHA licenses already. The family-owned company SECI plans to build a 5,000 t per year plant in Italy. The Russian firm TAIF took out a license to build a 10,000 t plant in the Republic of Tatarstan. Bio-on has also licensed its process to companies in France, Spain, and Mexico.
A few other firms are jumping into the business as well. Japan’s Kaneka is set to have 5,000 t of capacity for PHBH in Takasago, Japan, by the end of the year. CJ CheilJedang, with Metabolix’s technology in hand, plans to either build a pilot plant or outsource small-scale PHA production, Sim Do Yong, of the company’s business development team, tells C&EN. The company aims for commercial production in 2022.
RWDC Industries was cofounded by Daniel Carraway, who also founded Danimer but later left the company. It has raised $35 million from investors and plans to build a PHA plant in Athens, Georgia.
Mango Materials, meanwhile, has nearly completed a demonstration unit at the Redwood City site where it operates the pilot plant. The unit will run continuously and produce more than 100 kg of material per week. “We can derisk a few components of the technology while actually producing meaningful volumes of material to use it for applications,” Schauer-Gimenez says.
A commercial plant, she acknowledges, is still a few years away. Mango will soon close a fundraising round, Schauer-Gimenez says, with investors who appreciate the amount of time needed to get the technology off the ground.
“Patient capital is what’s really key for us right now,” she says. “We’re not an iPhone app. Your return doesn’t come overnight.”
No comments:
Post a Comment